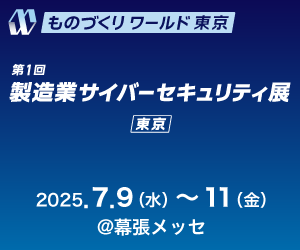
この度、2025年7月9日(水)〜11日(金)に幕張メッセで開催される第37回ものづくりワールド東京に出展することが決定いたしました!...
国内でも製造業のDXが推進され、製造現場でもデジタル技術を取り入れる動きが活発になりました。多くの製造業がスマートファクトリーと呼ばれる取り組みを行い、生産性の向上や品質向上、コスト削減などの課題を解決しています。とは言っても、スマートファクトリーの認知度は依然として低く、スマートファクトリーの取り組みができていない企業も多くあります。
今回は「今後取り入れるか検討中の方」や「製造現場の課題解決に向けて何かしらの取り組みを行いたい方」に向け、スマートファクトリーの概要から必要となった背景と目的、国内の導入事例を解説します。
目次
スマートファクトリーとは、AIやIoTなどのデジタル技術を活用することで、生産性の向上や効率化、省エネによる環境配慮を実現した工場を指します。デジタル技術を活用することで、工場の課題を一部だけ改善するのではなく、工場全体の課題をまとめて解決できる仕組みを実現できます。ビジネスの根本となる設計や製造、データ収集、データ活用など、従来の自動化に付加価値を加えた工場がスマートファクトリーと言えます。環境配慮にも長けており、自然エネルギーを活用した工場も注目を集めています。
スマートファクトリーが必要となった理由として、製造業の人材不足の解消や世界的に工場のグリーン化が求められていることが背景にあります。少子高齢化による人材不足は様々な業界の課題ですが、製造業においても例外ではありません。
国内における製造業の就業者数は、2002年の1202万人から2020年には1045万人と、約20年間で約157万人減少しました。全産業における製造業就業者の割合も減少傾向にあり、若年就業者数も、2002年の384万人から2020年の259万人へと、約20年間で約125万人減少しています。
こうした就業人口の減少を受け、採用を強化する元来の対策から、ロボットの導入による自動化と省人化、デジタル技術を活用した全行程の効率化に注目が集まりました。
また、日本を含めた124ヶ国では2050年までにカーボンニュートラルを目指すと表明しています。例えば、アメリカのApple社は、製品の製造時に使用する電力の100%を2030年までに再生エネルギーを利用すると目標を掲げており、大企業を中心に製造業のグリーン化が進んでいます。
グリーン化の観点では、日本でも地球温暖化対策に力を入れており、2019年度のCO2排出量は2013年度と比べ、17%の削減に成功しました。国内の二酸化炭素排出量は製造業が最も多く、現在も様々な取り組みでカーボンニュートラルを目指しています。
例えば、2021年末までに全製品の温室効果ガス排出量(カーボンフットプリント)を算出し、原材料の調達から出荷までの排出量を可視化できるようする取り組みがあります。
これらの問題に貢献できるため、スマートファクトリーが注目を集めるようになりました。
スマートファクトリーの動きは、国内だけでなく世界的に見ても活発です。例えば、ドイツでは製造業のオートメーション化やコンピュータ化を図る「industrie 4.0」が広がり、アメリカでは「IIC(Industrial Internet Consortium)」が設立されました。国内でも海外の動きに合わせ、経済産業省が「スマートファクトリーロードマップ」を2017年に発表し、製造業の世界的な変化に対応しています。
AIやIoT、ビッグデータなどのデジタル技術の進展、資源の制約、顧客ニーズの変化など、ものづくりを取り巻く環境は日々変化しています。ものづくりの20年から30年後の姿に向けて、製造現場の在り方を明確に示したものがスマートファクトリーロードマップです。
スマートファクトリーロードマップでは、スマート化の目的を7つ定めています。7つの項目に対応することが、製造現場のデジタル・ソフトウェア化に必要なのです。
スマートファクトリーでは、人が関わる作業において、作業手順やその結果などのデータを機器同士がリアルタイムで収集・分析することで品質の向上やトラブルの発生を最小限に抑えられます。品質の向上は「不良率の低減」「品質の安定化とばらつきの低減」「設計品質の向上」の3つの観点が重要です。作業者によって品質のばらつきに差があると、不良率にも影響を与えてしまいます。スマート化によって一定の品質を担保できれば、より高品質の製品を作れます。
スマート化による大きな目的はコストの削減にあります。製造業は「材料の使用量」「生産のための各種リソース」「余剰在庫」「設備管理」などのコストが発生しています。さらに、これらのコストを人の手で管理するとなると、より大きなコストがかかってしまいます。IoTやAIによるデジタル技術を導入することで、機器の稼働状況や在庫管理、従業員の負担、需給予測なども最適化できるため、効果的にコスト削減できます。
スマートファクトリーの最も大きな目的は生産性の向上です。生産性の向上は「設備や人の稼働率の向上」「作業の効率化・作業負担の軽減」「設備故障に伴う稼働停止の削減」の3つが掲げられています。コストの削減と同様に、デジタル技術を導入することで、一連の製造工程を効率化できます。その結果、人員配置を変えずとも業務効率や成果が上がった企業も数多くあります。
製品化と量産化の期間短縮とは「製品開発・設計の自動化」「仕様変更対応の迅速化」「生産ラインの設計・構築の短縮化」の3つの観点で実現します。
スマートファクトリーでは、ビッグデータの収集・分析が可能なので、設計から開発、量産化までのプロセスを最適化しやすいです。デジタル技術を組み合わせることで、これらのプロセスの一部または全てを自動化でき、生産速度を高速化できます。
人材不足と人材育成は多くの企業が抱える課題です。スマートファクトリーはこれらの課題の解決にも繋がります。実現方法は「多様な人材の活用」「技能の継承」の 2つが掲げられており、デジタル技術を導入することで、センサーによって熟練技術者の動きを分析したり、深い知見を全社で共有できるようになります。
その一方で、デジタルを意識した人材育成も必須となり、デジタルに強い人材を雇うか、教育の環境を整える必要が出てきました。
デジタル技術の急速な発展により、従来のサービスや製品に付加価値が要求されるようになりました。その結果、顧客は自分だけのオリジナル製品を求めるようになり、顧客ニーズが多様化しました。
スマートファクトリーでは、顧客ニーズに柔軟かつ迅速に対応します。デジタル技術を活用することが新たな付加価値と提供価値の向上に繋がります。
スマートファクトリーを導入したことで、これまでの課題を解決できた事例を紹介します。
ダイキン工業株式会社は、国内外に拠点を置く空調メーカーです。グローバル化を進めるにあたり、海外工場の熟練技術者不足が課題となっていました。そこで技能継承に焦点を当て、スマートファクトリーを推進することで「品質の向上」を目指しました。
日立製作所と協働し、作業工程のデジタル化と作業評価システムを開発したところ、課題となっていた技能継承に大きな効果が見込めました。このシステムは、熟練技術者の動きを計測・解析することで技能や効率性をデータ化します。その結果を8つの評価項目として数値化することで体系的に熟練技術者のノウハウとして活用されています。
今回は、スマートファクトリーの概要から必要となった背景と目的、国内の導入事例を解説しました。今では、製造業においてもデジタル技術を活用することが最低条件となりつつあります。今後の市場において、競争力を強化するためにもスマートファクトリーの取り組みは重要です。